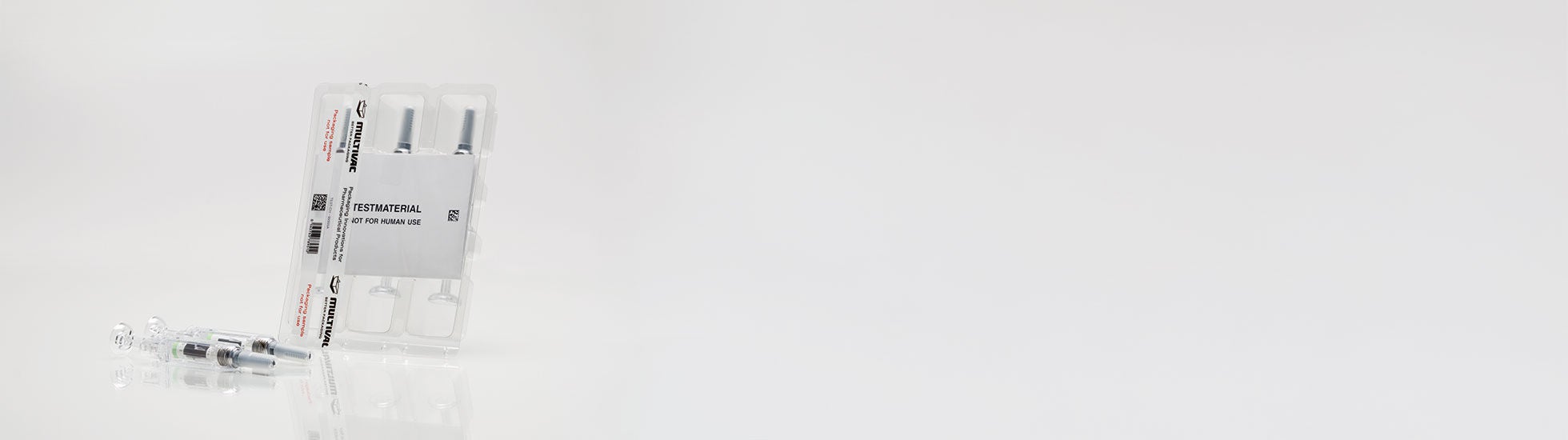
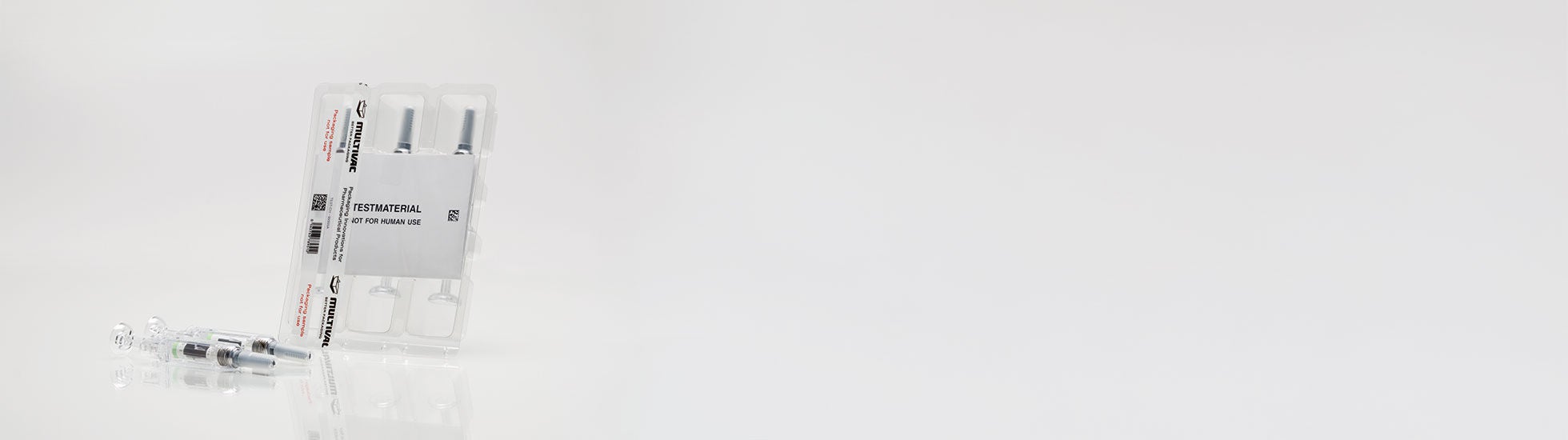
Abhängig von der jeweiligen Anwendung bietet MULTIVAC verschiedene Verpackungssysteme, die mit unterschiedlichen Zuführ- und Beladelösungen ausgestattet werden können, wie z. B. Tiefziehverpackungsmaschinen mit modularen Automatisierungslösungen, die es ermöglichen, verschiedene Produkte mit unterschiedlichem Durchsatz zu verpacken. Zu den Möglichkeiten der Produktzuführung zählen unter anderem eine lineare Vibrationszuführung, eine Universalzuführung über Bänder, Steigförderer, Zentrifugen oder der Transport mittels Werkstückträger.
Beim Herstellen von Kombinationspackungen für Pharmaprodukte hat oberste Priorität, dass die Packungen vollständig beladen und die einzelnen Komponenten in der Packung sicher geschützt sind. So dürfen Produkte, die mit aktiven Wirkstoffen befüllt sind, im Verpackungsprozess nicht beschädigt werden oder gar verloren gehen, und es muss vermieden werden, dass die Substanzen während des Verpackungsprozesses aktiviert oder miteinander vermischt werden. Weiterhin ist eine unabdingbare Anforderung, dass beschädigte Produkte sicher aus dem Verpackungsprozess ausgeschleust werden.
In Abhängigkeit der Produktbeschaffenheit bedarf daher bereits das Separieren und Ausrichten der Produkte während des Zuführprozesses unterschiedlicher Systeme und Prozesse. So können beispielsweise Teile, die als Bulkware angeliefert werden, über Vibrationstöpfe separiert und orientiert werden, während befüllte Spritzen üblicherweise auf Träger- oder Bandsystemen zugeführt werden. Das Beladen der Packungskavitäten mit den jeweiligen Produkten erfordert Beladesysteme, die die Aufnahme, das Ablegen und die genaue Positionierung in der Packungskavität sicherstellen.
Eine typische Anwendung ist die Verpackung mehrerer Produkte – zusammen mit einem Leaflet in einer komplex ausgeformten Kombinationspackung. Dabei wird ein Höchstmaß an Prozesssicherheit gefordert. Zudem erwarten immer mehr Hersteller Lösungen aus einer Hand, in die auch Module von Drittanbietern eingebunden werden können. Mit seiner ausgeprägten Linien- und Automatisierungskompetenz ist MULTIVAC hierfür der richtige Partner.
Üblicherweise werden die Kombinationspackungen aus Produktkomponenten zusammengesetzt, die aus Materialien unterschiedlicher Beschaffenheit bestehen, wie zum Beispiel weiche, harte, haftende oder nicht haftende Materialien. Jede einzelne Komponente muss schonend und sicher an der dafür vorgesehenen Position in der Packung abgelegt werden. Deshalb wird die Tiefziehform mit unterschiedlichen Kavitäten ausgestattet, in denen die Produkte richtig positioniert und fixiert werden können. Die passgenaue Ausformung der Packungskavität kann beispielsweise durch den Einsatz eines Formsystems mit Stempelunterstützung optimiert werden. Das Einlegen der Produktkomponenten erfolgt in der Regel automatisiert, um eine hohe Prozesssicherheit zu gewährleisten.
Bei der Entwicklung einer entsprechenden Verpackungslösung müssen zudem folgende Anforderungen berücksichtigt werden: Neben der Vollständigkeit der Packung muss sichergestellt werden, dass die sensiblen Produkte fest in der Packung fixiert sind und nicht verrutschen können. Insbesondere bei hochwertigen Produkten muss gewährleistet sein, dass diese während des Verpackungsprozesses nicht verloren gehen. Zudem müssen die Vollständigkeit der Kombinationspackung und das Druckbild auf der Oberfolie im Verpackungsprozess prüfbar sein.
Anhand des folgenden Beispiels wird der Herstellprozess einer Kombinationspackung mit unterschiedlichen, kleinen Komponenten erläutert.
Ein Teil der Produkte wird als Bulkware angeliefert und über eine Universalzuführung zum Handhabungsmodul transportiert. Dabei separiert eine „Bürste“, die über dem Transportband rotiert, die teilweise aneinanderhängenden oder übereinanderliegenden Produkte, sodass sie nunmehr vereinzelt auf einem Transportband liegen. Die Position und Orientierung der Produkte wird über ein Vision-System erfasst und an den Greifer des Pick-&-Place-Roboters gemeldet. Dieser übernimmt mit Sauggreifern die Produkte vom Transportband und legt sie in der dafür vorgesehenen Packungskavität ab. Alle Produkte, die der Greifer nicht aufnimmt, fallen in einen Sammelbehälter und werden dem System wieder zugeführt.
Eine weitere Komponente wird ebenfalls als Bulkware angeliefert, diese wird jedoch über einen Steigförderer in eine Zentrifuge transportiert. In dieser Zentrifuge werden die einzelnen Produkte separiert und orientiert. Über ein Schienensystem gelangen sie dann in einen Drehteller, auf dem jeweils zwei Produkte abgelegt werden können. Der Teller dreht sich dabei abwechselnd nach links und rechts, wobei bei jeder Drehbewegung ein Produkt in den Teller gespendet wird. Dabei überprüfen Lichtsensoren die Anwesenheit der Produkte. Schließlich nimmt ein Sauggreifer die Produkte von diesem Teller und positioniert sie in der jeweiligen Kavität. Während dieses Pick-&-Place-Vorganges dreht sich der Teller und ein neues Produkt liegt zur Abholung bereit.
Vor der Beladung einer weiteren, hochwertigen Produktkomponente in die Packung erfolgt eine Anwesenheitskontrolle der beiden anderen Produkte mittels eines Vision-Systems. Nur wenn diese beiden Komponenten vollständig in die Packung eingelegt und auch korrekt positioniert wurden, erfolgt das Einlegen der hochwertigen Produktkomponente in die Packung. Diese wird mit einem Steigförderer angeliefert und über Vibrationsschienen separiert. Durch ein Schienensystem werden die Produkte in eine hängende Position orientiert und weitertransportiert. Eine 90°-Umlenkschiene sorgt dafür, dass die Produkte am Ende wieder liegend und dabei alle in gleicher Ausrichtung positioniert sind. So können sie durch ein Spendersystem einzeln von einer Trägerplatte entnommen und in der Packungskavität abgelegt werden. In der Zwischenzeit wird ein neues Produkt in Position gebracht. Abschließend erfolgt das automatisierte Einlegen des Leaflets über einen Leaflet-Dispenser, damit ist die Packung vollständig.
Eine wichtige Anforderung solcher automatischer Verpackungsprozesse ist die Möglichkeit, bei Bedarf manuell in den Prozess eingreifen zu können und die Produkte nachträglich korrekt zu positionieren. Hierfür werden die Verpackungslinien üblicherweise so konzipiert, dass nach den automatisierten Beladestationen ausreichend Platz für das manuelle Beladen beispielsweise von fehlenden Produkten eingerichtet wird.
Die Visualisierung der einzelnen Gut- und Schlechttakte erfolgt durch farbige Lichtsignale, die in Form von im Rahmen verbauten Lampen visualisiert werden: Grünes Licht bedeutet einen Guttakt, rotes Licht einen Schlechttakt. Grund für einen Schlechttakt kann zum Beispiel eine unvollständig ausgeformte Packungskavität sein. Aber auch wenn die Folie zu lange unter der heißen Heizplatte verweilte (Verweildauerüberwachung) oder ein Produkt fehlt, wird dies dem Bedienpersonal durch ein rotes Licht angezeigt.
Sind die Packungen schließlich korrekt und vollständig beladen, werden sie der Siegelstation zugeführt. Als Oberfolie kann unbedrucktes Papier, Tyvek® oder Kunststofffolie zum Einsatz kommen. Unmittelbar vor dem Versiegeln kann die Oberfolie durch einen Thermotransfer-Drucker mit variablen Daten wie beispielsweise Lot-Nummer, Produktionsdatum etc. bedruckt werden. Auch in diesem Bereich kommt ein Vision-System zum Einsatz, das nach dem Versiegeln das Druckbild auf Anwesenheit, Lesbarkeit und Korrektheit prüft.
Nach dem Siegelprozess erfolgt die Vereinzelung der Packungen mittels Quer- und Längsschneidung. Anschließend werden die fertigen Einzelpackungen über einzelne Gurtbänder weitertransportiert und von einem Handhabungsmodul aufgenommen. Um den Footprint der Verpackungslösung zu optimieren, kann dieses Modul in die Verpackungsmaschine integriert und auf den Maschinenrahmen aufgesetzt werden. Die Sauggreifer entnehmen ausschließlich die Gutpackungen von den Bändern und setzen sie auf ein weiteres Band um, das im 90°-Winkel angeschlossen ist. Die Entnahme erfolgt dabei auf Einzelpackungsebene. Anschließend transportiert das Band die Gutpackungen zum nächsten Prozessschritt, in der Regel ist dies das Umsetzen der Sekundärverpackung in Umkartons. Die Schlechtpackungen laufen über Einzelbänder aus der Linie und werden in einer Abfallbox gesammelt. Eine Streckensteuerung sorgt dabei für das sichere Ausschleusen von niO-Packungen ebenfalls auf Einzelpackungsebene. Die Entnahme der Gutpackungen entspricht der sogenannten „good philosophy“ – sie garantiert, dass keine Schlechtpackungen in den Gutpackungen sein können.
Um Anforderungen der Pharmabranche hinsichtlich der Prozess- und Packungssicherheit vollumfänglich zu erfüllen, kann die Verpackungslösung mit weiteren Features ausgestattet werden. So kann die Linie komplett mit transparenten Polycarbonat-Elementen eingehaust werden, deren großflächige Türen sich leicht öffnen lassen. Damit ist der gesamte Prozess GMP-konform – das Bedienpersonal kann die Maschineninnenräume gut einsehen und verloren gegangene Produkte rasch erkennen und entfernen. Im Sinne einer verlässlichen Line Clearance wird sichergestellt, dass keine Substanzen oder Produkte nach Chargenende in der Anlage verbleiben, das Risiko einer Kontamination oder eines Maschinenstopps ist daher sehr gering.
Darüber hinaus kann die Tiefziehverpackungsmaschine zusätzlich mit elektrisch aufklappbaren Werkzeugoberteilen an der Form- und Siegelstation ausgestattet werden. Sie ermöglichen eine genaue Untersuchung der Werkzeuge auf etwaige Beschädigungen oder Verschmutzungen. Und nicht zuletzt überprüfen die eingesetzten Vision-Systeme, ob die Packungen vollständig und korrekt beladen und die Kennzeichnungen fehlerfrei sind.
10.06.2018