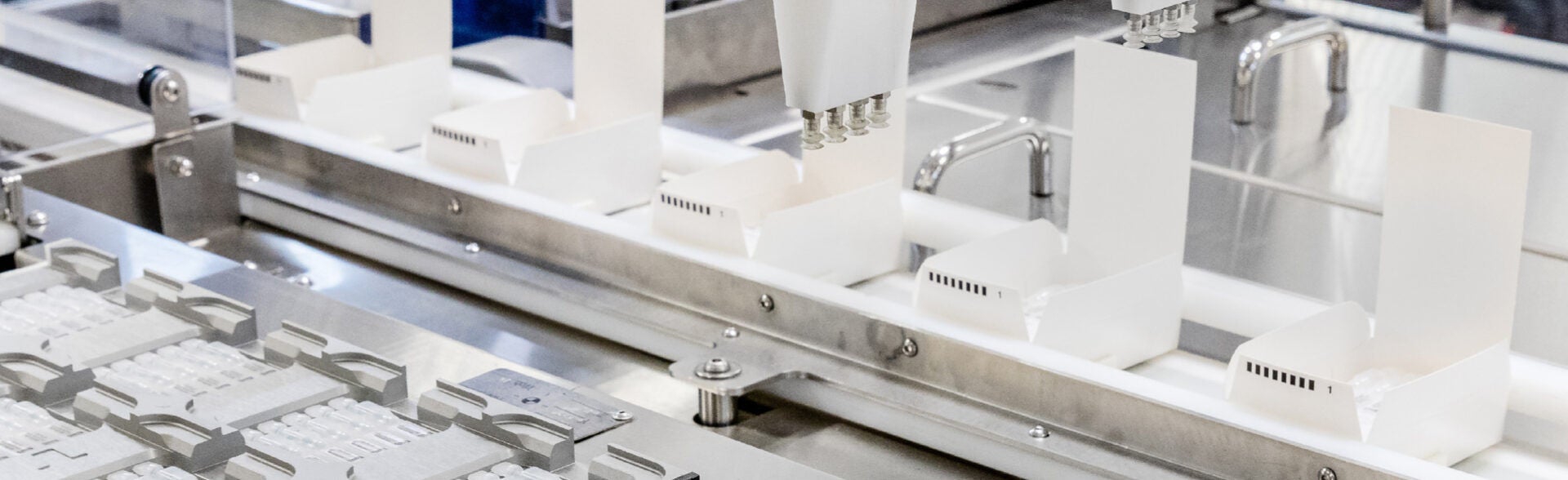
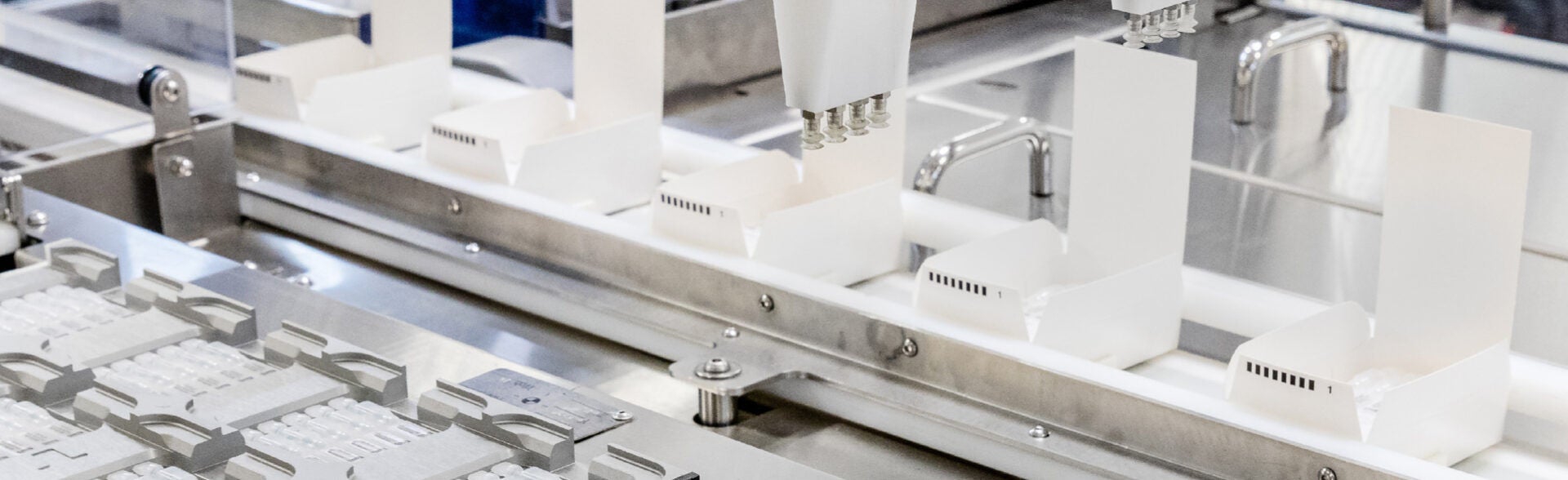
Automatisierung spart Kosten. Denn in der Regel wird für den Betrieb von automatisierten Prozessen weniger Personal benötigt als bei der Durchführung von manuellen Prozessen. Vor allem aber erhöht die Automatisierung die Prozesssicherheit, reduziert Fehlerquoten und verbessert auch maßgeblich die Hygiene, da sie zu einer signifikanten Reduzierung der Kontaminationsmöglichkeiten beiträgt.
Automatisierungskomponenten können sich zudem auch hinsichtlich der Aspekte Ergonomie und Arbeitssicherheit positiv auswirken, etwa durch den Einsatz von Handhabungsmodulen, die schwere Produkte automatisch aufnehmen und präzise ablegen. Ein weiterer Vorteil insbesondere mit Blick auf die Produktqualität und Produktsicherheit bietet sich durch den Einsatz von Systemen, die instabile – rollende wie auch nicht stehende - Produkte schonend und sicher durch den gesamten Verpackungsprozess transportieren.
Insbesondere bei der Beladung, der Orientierung und dem Transport von sensiblen Medizin- und Pharmaprodukten lässt sich erhebliches Optimierungspotenzial ausschöpfen. So können beispielsweise flexible Greifersysteme eingesetzt werden, die in der Lage sind, jedes einzelne Produkt zu erfassen, ohne es zu beschädigen - ein wichtiger Faktor hinsichtlich der Qualität wie auch der Produkt- und Prozesssicherheit. Zudem gewährleisten die Systeme die optimale Orientierung der Produkte für den nachfolgenden Prozessschritt und legen diese sicher und vor allem exakt in die vorgesehene Packungsmulde ab.
Für einen schonenden Transport sorgen neben unterschiedlichen Bandsystemen auch die sogenannten Carrier Konzepte. Als Carrier wird dabei eine Art Werkstückträger bezeichnet, der beispielsweise die zu verpackenden Produkte während der Assemblierungsschritte transportiert und nach der fertigen Assemblierung zum Verpackungsprozess bringt. Auch für den Transport von empfindlichen Gütern, die nicht im Bulk verpackt, transportiert oder gelagert werden dürfen, kommt ein solches Konzept in Frage – ebenso wie für Produkte aus Glas, die transportiert und verpackt werden müssen, ohne dass es zu einem unerwünschten Glas-Glas-Kontakt kommt.
Die Bandbreite an Produkten, für die sich Carrier Systeme als Transportlösung eignen, ist groß – sie reicht von vorgefüllten Spritzen und anderen Behältnissen mit Wirkstoff, die Teil einer Kombinationspackung sind, über assemblierte Komponenten wie Injektoren, Schlauchsets, Katheter und Nahtmaterial bis hin zu Augentropfen-Ampullen aus Kunststoff. Ebenso kann das Carrier System auch für den Transport von vorgeformten Trays ohne Inhalt sowie von vorgeformten Trays nach der Produktbeladung hin zum Siegelprozess als auch von fertig versiegelten Packungen zur danach folgenden Sekundärverpackung genutzt werden.
Die Systeme lassen sich bei Tiefziehverpackungsmaschinen wie auch bei Traysealern einsetzen – in Kombination mit Traysealern sind dabei auch kleine Losgrößen bis hin zu Losgröße 1 realisierbar. Dabei erfolgt die Beladung der Packungsmulden hocheffizient an einer definierten Position, wobei in einem Zyklus auch mehrere Produkte gleichzeitig beladen werden können.
Dank ihrer Modularität sind Carrier Systeme hinsichtlich ihres Layouts sehr flexibel. Sie passen sich den Produktionsumgebungen perfekt an und können in unterschiedliche Richtungen in einem geraden oder auch mit einem runden Verlauf geführt werden.
Damit schafft der Carrier eine Verbindung zwischen unterschiedlichen Prozessschritten und ermöglicht einen kontrollierten Transport der Produkte oder Packungen entlang der Prozesskette. Carrier Konzepte zeichnen sich darüber hinaus durch weitere Vorzüge aus, etwa in Bezug auf die Prozessgeschwindigkeit aufgrund der gleichzeitigen Beladung von Produkten oder auch Packungen in einem Werkstückträger. Zudem sorgen klar definierbare Schnittstellen, auch zu vorgeschalteten Prozessen, für eine hohe Prozesssicherheit.
Wird zudem eine Pufferfunktion integriert, lassen sich Stopps im Prozess etwa durch den Ausfall eines vor- oder auch nachgelagerten Prozesses problemlos überbrücken, die Prozesse dadurch entkoppeln und ein kontinuierlicher Produktfluss sicherstellen. Dies ist von erheblicher Bedeutung, da solche Stopps in automatisierten Lösungen nicht selten zu erheblichen Effektivitätsverlusten der gesamten Linie führen können.
Ein gängiges Anwendungsfeld für Carrier Systeme ist zum Beispiel eine Produktionsumgebung, in der zwischen dem vorgeschalteten Prozess und der Beladung der Packungskavitäten mit den Produkten keine unmittelbare Verbindung besteht. In diesem Anwendungsfall können die Produkte während oder nach der Assemblierung mittels Werkträger kontrolliert der Verpackungsmaschine zugeführt werden. Auch die Beladung der Produkte in Faltschachteln ist denkbar. Das Layout des Carriers kann hierbei flexibel gestaltet und an die zur Verfügung stehende Fläche adaptiert werden. Möglich ist die Lösung sowohl im Zusammenspiel mit einem Traysealer als auch mit einer Tiefziehverpackungsmaschine.
Mit Hilfe des Carrier Systems können auch mehrere Komponenten gleichzeitig transportiert werden, ohne dass empfindliche Produkte, wie etwa Glasspritzen, im Werkträger während des Transportes zur nachgelagerten Station durch gegenseitigen Kontakt beschädigt werden. Die Assemblierung der Produkte erfolgt in einem vorgelagerten Schritt und zwar in den Werkstückträger, in dem sie an die nachgelagerte Verpackungsmaschine transportiert werden. Sie sind dann bereits so angeordnet, also separiert und orientiert, dass sie beispielsweise von einem Greifer direkt aufgenommen und in der entsprechenden Packungsmulde abgelegt werden können. Der Carrier übernimmt während des Transportes zudem eine Pufferfunktion und kann somit Mikro-Stopps und Störungen ausgleichen. Durch intelligent eingesetzte Pufferfunktionen lässt sich gar ein kompletter Stillstand in unterschiedlichen Teilprozessen verhindern.
Sinnvoll lässt sich ein Carrier Konzept auch in Kombination mit einem vollautomatischen Traysealer, etwa einem T 700 von MULTIVAC, einsetzen. Vorgeformte Trays mit zum Teil mehreren Kavitäten werden dabei entweder manuell oder automatisiert zum Beispiel mittels eines MULTIVAC Tray Denesters in den Tray Carrier gespendet und über Bandsysteme zur Verpackungsmaschine transportiert. Die Trays können dabei aus verschiedenen Materialien bestehen – ein gängiges Beispiel sind APET-Blister, die mit Deckelfolien aus Papier oder Tyvek® verschlossen werden. Ihre Kavitäten sind so ausgeformt, dass die einzelnen Produkte in dem Tray fixiert werden, so dass sie weder verrutschen noch mechanisch beschädigt werden können.
Auf dem Zuführband des Traysealers erfolgt dann das automatisierte Beladen der Produkte in diese vorgeformten Trays, wobei die zu verpackenden unterschiedlichen Komponenten durch individuell auf das jeweilige Produkt ausgelegte Systeme an die Maschine herangeführt werden. Vorgefüllte Spritzen werden zum Beispiel auf Werkstückträgern transportiert. Kleine Komponenten wie Kappen, Hülsen oder Nadeln gelangen in der Regel als Bulkware zu einem Vibrationstopf, wo sie separiert und ausgerichtet werden. Produkte, die von einem vorgeschalteten Prozessschritt wie einer Kennzeichnungslösung kommen, lassen sich über eine Rollenbahn oder ein Bandsystem zuführen.
Die Beladung der Werkstückträger erfolgt üblicherweise mittels Pick-and-Place-Lösungen Hierfür werden modulare Handhabungsmodule von MULTIVAC in Abhängigkeit von Produkt und erforderlicher Taktzahl mit einem oder mehreren Robotern ausgestattet. Sie nehmen mit passenden Greifern die jeweiligen Produkte auf und legen sie zuverlässig in der entsprechenden Kavität des Trays ab.
Die befüllten Trays, die aufgrund ihrer komplexen Ausformung oftmals nicht selbststehend sind, werden schließlich mit dem Carrier zur Siegelstation und anschließend zur Packungsentnahme transportiert. Dort entnimmt ein Handhabungsmodul die versiegelten Packungen aus dem Carrier. Je nach Anforderung erfolgt die Entnahme der Packungen einzeln oder zu mehreren Packungen gleichzeitig.
Der Vorteil dieses individuell konfigurierbaren Rundläufersystems, das mittels mehreren Carriern erst die leeren Trays zur Beladung und dann die gefüllten Trays bis zum Ende der Verpackungslinie führt, besteht in seiner hohen Flexibilität. Denn es ist sowohl für die individuelle Fertigung in sehr kleinen Losgrößen, auch ab Losgröße 1, bis hin zur Produktion von höheren Stückzahlen nutzbar. Bei kleineren Stückzahlen kann das Beladen manuell, bei höheren Stückzahlen auch automatisiert erfolgen. Für das Fertigen von Kleinstserien kann das zirkulierende Trägersystem mit nur einem Tray Carrier, für höhere Taktraten mit mehreren Tray Carriern bestückt werden.
In Abhängigkeit der Investitionsbereitschaft wie auch der individuellen Anforderungen des Unternehmens lässt sich das Konzept schrittweise realisieren bzw. der Automatisierungsgrad erhöhen. Die Modularität ermöglicht also den sukzessiven Ausbau der Automatisierung in verschiedenen Stufen bis hin zu einem ganzheitlichen Verpackungskonzept, bei dem alle Komponenten perfekt aufeinander abgestimmt und über ein einheitliches Bedienkonzept sicher steuerbar sind.
Des Weiteren können Carrier Konzepte auch beim Verpacken von Produkten, die unkontrolliert aus dem der Verpackungsmaschine vorgelagerten Prozessschritt gelangen, zum Einsatz kommen. Das Tray Carrier System ermöglicht hierbei einen kontrollierten Transport der Produkte mittels Werkstückträgern zur Verpackungsmaschine. Ein Beispiel sind Augentropfen-Ampullen aus Kunststoff, die üblicherweise unkontrolliert aus dem der Verpackungsmaschine vorgelagerten Prozessschritt bereitgestellt werden.
Auch bei diesem Szenario ist die Implementierung einer integrierten Pufferfunktion sinnvoll, um Mikro-Stopps oder gar längere Ausfälle zu überbrücken. Das Carrier System kann dabei die Werkstückträger bei etwaigen Störungen in einem Pufferturm oder auch in mehreren Puffertürmen unterbringen. Sofern die Linie beispielsweise mit zwei Puffertürmen ausgestattet wird, kommt der erste Pufferturm sinnvollerweise nach dem Beladen der Plastikampullen in die Träger zum Einsatz. Hier können die befüllten Träger gepuffert werden, falls eine nachgelagerte Maschine, etwa ein Etikettierer, eine Tiefziehverpackungsmaschine oder ein Kartonaufrichter, ausfällt. Sobald ein beladener Träger in den ersten Pufferturm gelangt, wird aus dem zweiten Pufferturm ein leerer Träger nachgeführt, um ein geschlossenes System zu gewährleisten, in dem die einzelnen Werkstückträger in Umlauf gehalten werden.
Eine weitere Anwendung für Carrier Systeme ist die Assemblierung von fertigen Produkten in einem geschlossenen Prozess. Dies können beispielsweise vorgefüllte Spritzen sein, die in einem vorgelagerten Prozess assembliert werden und separiert und orientiert in einem Werkstückträger platziert werden. Dieser Carrier wird dem Verpackungsprozess über Bänder kontrolliert zugeführt, dabei kann er auch als Transportverpackung dienen. An der Verpackungsmaschine übernimmt ein Greifer die Produkte aus den Trägern und legt diese einzeln oder auch vorgruppiert in die Packungskavitäten.
Bedarfsgerechte und damit vor allem auch wirtschaftliche Lösungen für nahezu alle Anforderungen in der Medizingüter-, Kosmetik- und Pharmaindustrie bietet MULTIVAC mit seinen unterschiedlichen Automatisierungslösungen und insbesondere mit seinen individuell auslegbaren Carrier Konzepten. Die ausgeprägte Automatisierungs-, System- und Anwendungskompetenz des Marktführers erlaubt dabei stets einen ganzheitlichen Ansatz, das umfassende Portfolio die Realisierung auch hochkomplexer Projekte mit optimal aufeinander abgestimmten Komponenten aus einer Hand. Eine durchgehende Streckensteuerung, die alle Linienmodule einbezieht, gewährleistet einen sicheren Prozess sowie ein Maximum an Effizienz und Transparenz bei geringstmöglichem Aufwand und optimalem Produktfluss. Jedes Produkt, jede Verpackung wird permanent überwacht, Fehler sogleich erkannt.
10.03.2020