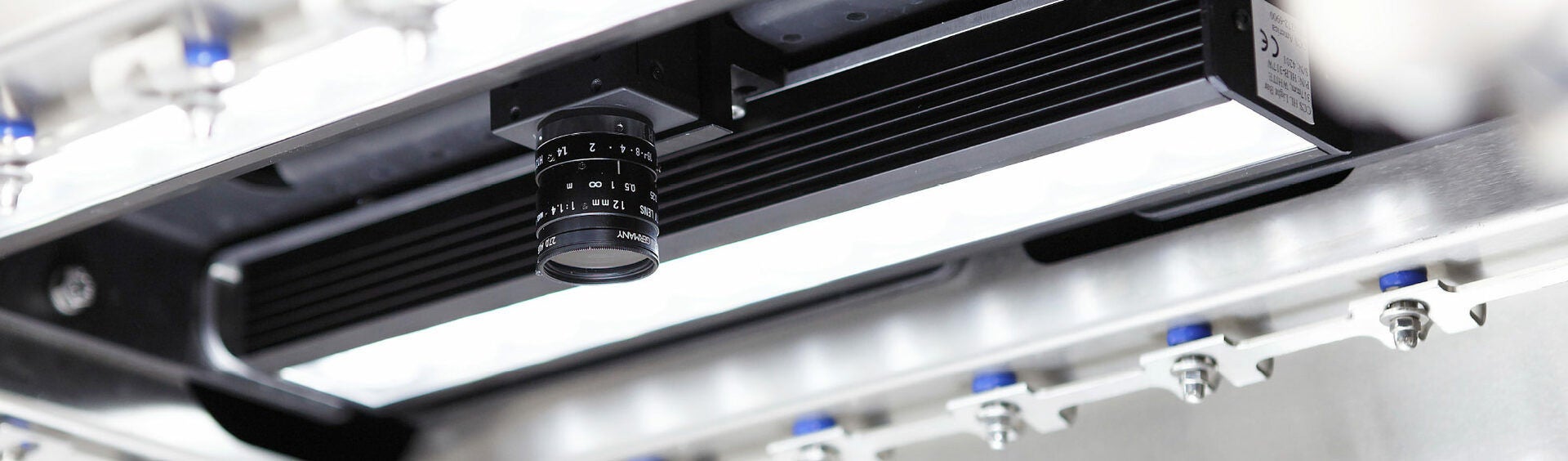
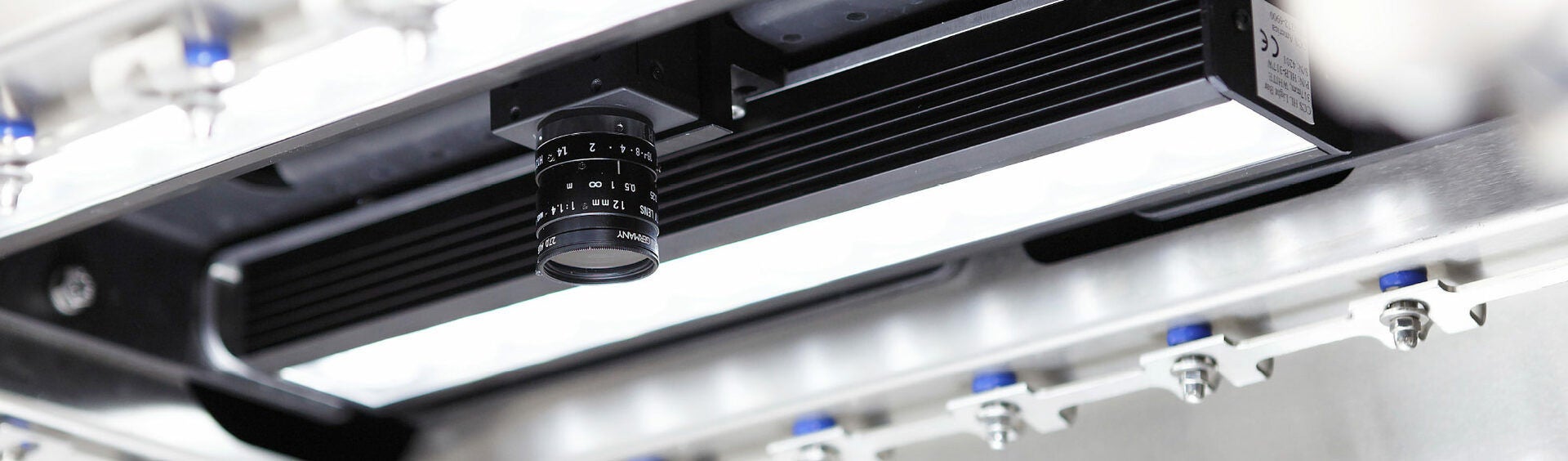
Höhere Ausstoßkapazitäten bei geringerem Personalbedarf sowie Verbesserungen hinsichtlich der Ressourcen- und Kosteneffizienz tragen maßgeblich dazu bei, dass Investitionen in automatische Verpackungslösungen wirtschaftlich sinnvoll erscheinen. Aber auch Aspekte wie eine gleichbleibend hohe Verpackungsqualität und ein attraktives Verpackungsdesign zählen zu den relevanten Faktoren – schließlich tragen diese am Point of Sale zu einer Differenzierung gegenüber Wettbewerbsprodukten und dadurch zu einem höheren Absatz bei. Inspektionslösungen hingegen haben keinen unmittelbaren Einfluss auf das Produkt oder die Verpackung und auf den Erfolg desselben am Point of Sale.
Zur Erfüllung von gesetzlichen Vorgaben in Bezug auf Verbraucherinformationen und Rückverfolgbarkeit ist die Sicherstellung einer korrekten und einwandfrei lesbaren Kennzeichnung jedoch unabdingbar. Die stetig steigenden Anforderungen im Bereich der Lebensmittelkennzeichnung führen dabei zu einer entsprechend höheren Komplexität der Etiketten.
So müssen EU-weit alle Pflichtangaben laut Lebensmittel-Informationsverordnung (LMIV) in einer definierten Mindestgröße abgedruckt werden. Neben einer Zutatenliste umfassen diese Pflichtangaben unter anderem das Mindesthaltbarkeitsdatum, die Kennzeichnung von Allergenen wie auch eine verbraucherfreundliche Nährwerttabelle in einem exakt definierten Format. Hinzu kommt eine Vielzahl weiterer Elemente wie Chargennummern für die Rückverfolgbarkeit, unterschiedlichste Gütesiegel und Logos, Barcodes für Scannerkassen und auch QR-Codes, mit denen Konsumenten weiterführende Produkt- oder Gebrauchsinformationen über ihr Smartphone abrufen können.
Erhöht wird die Komplexität darüber hinaus durch den Trend hin zu einer stetig steigenden Produkt- und Variantenvielfalt sowie durch die Anforderung, die Informationen auf den Etiketten in mehreren Sprachversionen abzubilden, die unter Umständen schwer auseinanderzuhalten sind.
Parallel zur stetig steigenden Komplexität der Lebensmittelkennzeichnung wächst der Druck auf die Lebensmittelhersteller insbesondere im Exportgeschäft. Kennzeichnungsfehler wie nicht lesbare Barcodes, fehlerhafte Haltbarkeitsdaten oder gar falsche Produktetiketten können zu Retouren kompletter Lieferungen führen. Den Herstellern entstehen hierdurch unter Umständen erhebliche direkte und indirekte Kosten, die von Logistik- und Entsorgungskosten über Kosten für eine etwaige Nachproduktion bis zur Schädigung der Reputation reichen können. Bei schweren Verstößen drohen nicht selten Vertragsstrafen oder gar die Auslistung der betroffenen Produkte. Aber auch Schönheitsfehler wie nicht optimal ausgerichtete Etiketten zeigen Wirkung, denn sie schaden dem Markenimage, indem sie dem Verbraucher eine geringere Produktqualität und Sorgfalt beim Verarbeiten und Verpacken der Ware suggerieren.
Doch auch wenn Kennzeichnungsfehler bereits in der Produktionsstätte entdeckt werden, kann dies einen erheblichen internen Bearbeitungsaufwand nach sich ziehen. So sind Verpackungslinien häufig durchgängig bis zur Sekundärverpackung automatisiert. Wird beispielsweise erst in einem der letzten Prozessschritte bei einer Stichprobe ein Fehler entdeckt, kann bereits die gesamte Charge unbrauchbar sein oder zumindest eine Nachbearbeitung erfordern. Es gilt daher die Faustregel, dass Qualitätskontrollen so früh wie möglich im Prozess implementiert werden sollten.
Um sicherzugehen, dass tatsächlich nur einwandfreie Verpackungen in den Verkauf gelangen, sollte die Qualitätskontrolle auf Einzelpackungsebene erfolgen, wobei für eine hundertprozentige Sicherheit stichprobenartige Kontrollen in industriellen Produktions- und Verpackungsprozessen heute nicht mehr ausreichend sind. Durch die im Zuge der Automatisierung zunehmende Leistungsfähigkeit der Verpackungslinien ist eine umfassende Etikettenprüfung während des laufenden Verpackungsprozesses für das menschliche Auge nicht mehr möglich. Daher kommen Lebensmittelhersteller bei schnellen Taktraten heute nicht umhin, die Qualitätskontrollen mithilfe automatisierter Inspektionssysteme umzusetzen.
Zur Feststellung der Etikettenanwesenheit lassen sich zum Beispiel Lumineszenz-, Farb- oder Kontrastsensoren einsetzen. Aber auch Barcodescanner und Codeleser überprüfen implizit die Anwesenheit des Etiketts und kontrollieren darüber hinaus auch die Lesbarkeit des Barcodes. Außerdem wird der Inhalt des Codes analysiert und mit entsprechenden Referenzdaten verglichen.
Bei komplexen beziehungsweise multifunktionalen Inspektionsaufgaben von der Text- und Mustererkennung bis hin zu einer umfassenden Bildanalyse sind hingegen PC-basierte Matrix- oder Zeilenkamerasysteme wie das MULTIVAC MVS das Mittel der Wahl. So überprüft zum Beispiel die leistungsfähige Inspektionslösung I 420 auf einer Tiefziehverpackungsmaschine die Kennzeichnung mittels Texterkennung oder Textverifizierung auf Lesbarkeit und Inhalt der Codes. Auch die Etikettenposition und -ausrichtung sowie die Form des Etiketts und definierte Mustermerkmale werden erkannt. Soll eine Druckkontrolle mittels eines kamerabasierten Inspektionssystems erfolgen, kann MULTIVAC seine Kunden auch mit einer sogenannten „Optical Character Recognition (OCR) Spezifikation“ unterstützen. Die darin definierten maßgeblichen Mindestanforderungen bezüglich Schriftarten, Zeilenabstand, Ruhezonen, Kontrast und anderer relevanter Parameter gewährleisten die einwandfreie Maschinenlesbarkeit und damit die hundertprozentig zuverlässige Prüfbarkeit des Etiketts.
Hinsichtlich der Integration der Inspektionslösungen in die jeweilige Verpackungslinie ergeben sich je nach Anwendungsfall mehrere Möglichkeiten: Erfolgt die Kennzeichnung der Verpackung beispielsweise durch einen Querbahnetikettierer, kann die Kennzeichnungskontrolle direkt am Auslauf der Verpackungsmaschine installiert werden. Ebenso lassen sich optische Inspektionssysteme in Transportbandetikettierer oder aber unabhängig von Verpackungs- oder Kennzeichnungssystemen zum Beispiel als eigenständige End-of-Line-Lösung im Anschluss an einen Traysealer einbinden. Auch eine Nachrüstung von Inspektionslösungen in eine bereits bestehende Verpackungslinie ist in der Regel problemlos möglich.
Die ganzheitliche Liniensteuerung bietet darüber hinaus noch weitere Vorteile. So kann eine vollständig eingebundene Inline-Qualitätsinspektion das automatische Ausschleusen von Schlechtpackungen initiieren und auch die Nachjustierung von Modulen im laufenden Prozess erleichtern. Wird beispielsweise eine schleichende Verschlechterung des Druckbildes oder eine graduell ansteigende Verschiebung eines Etiketts festgestellt, kann an der entsprechenden Stelle gegengesteuert werden, bevor das Kennzeichnungsergebnis den Toleranzbereich verlässt. Schlechtpackungen können so nicht nur zügig erkannt, sondern eventuell sogar gänzlich vermieden werden.
Als ganzheitlicher Lösungsanbieter verfügt MULTIVAC über umfassende Erfahrungen im Bereich der optischen Inspektionssysteme sowie deren nahtloser Integration in Verpackungslinien. Die breite Anwendungskompetenz ermöglicht es, Kunden umfassend zu beraten und gegebenenfalls mit Sonderprogrammierungen auf spezifische Kundenanforderungen einzugehen. Insgesamt betrachtet bietet eine automatisierte optische Kennzeichnungskontrolle Mehrwert und Sicherheit in vielerlei Hinsicht, wobei sich die Investition je nach Umfang der jeweiligen Inspektionslösung unter Umständen bereits sehr schnell amortisiert.
27.02.2020