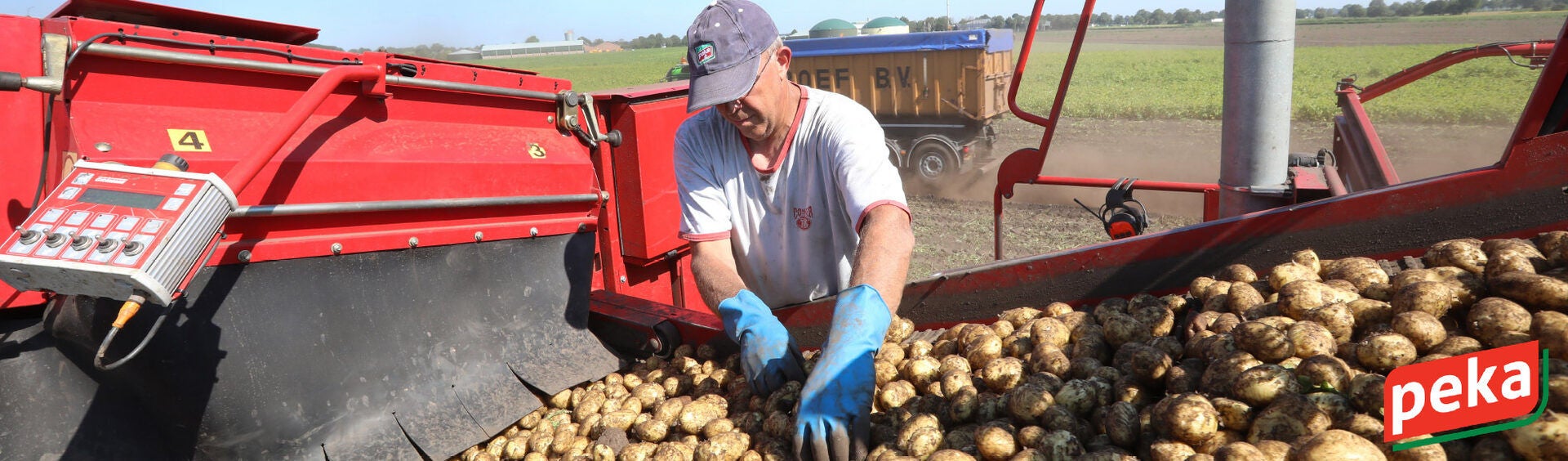
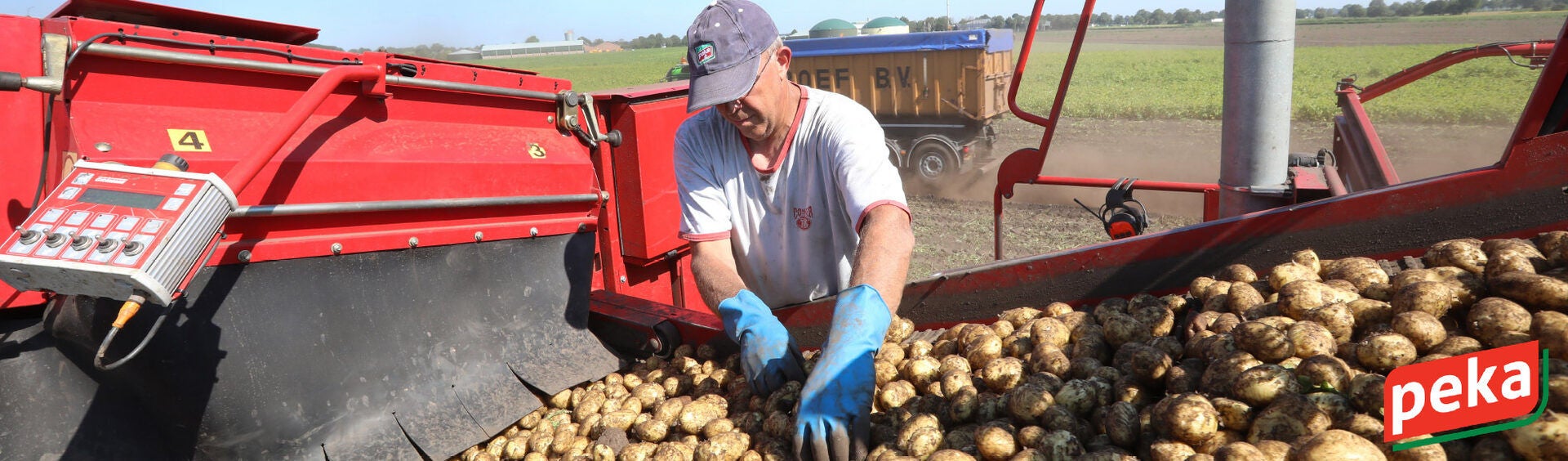
Product quality and pack security hold prime position at Peka Kroef BV in the Dutch town of Odiliapeel. The company, which with its 320 employees and turnover of some 100 million euros is today one of the leading suppliers of potato specialities, has “its roots literally in the soil”, as Frans Habraken, Corporate Engineering and Maintenance Manager, at Peka Kroef explains.
The business idea came originally from Piet Kroef. After the Second World War he saw his future as being in the potato trading business, since the family did not have sufficient land for potato cultivation. While Piet's son Gerard was successfully involved in the potato business in Berlin and Düsseldorf, Piet and his other sons concentrated in the Netherlands on the large-scale processing of mechanically peeled potatoes, since they wanted to serve the strong demand for pre-processed products in the salad industry. That was 1970 - and the Kroef family was among the early "peel pioneers".
Since the middle of the 1970's the process has developed into the steam peeling and cooking of the potatoes, then later vacuum packing and pasteurising. This reduced the time and effort significantly, and it was also possible to extend the shelf life of the products. In short, the foundation stone had been laid for the expansion of the business in both the range of products and the company's sales areas. During the 1980's Peka Kroef gradually advanced to market leader in supplying the entire salad industry. The introduction in 1996 of the "Peka Freshline" product range for the food service sector was another important step - and also the right response to a changing market situation and greater quality awareness by consumers.
From the beginning Peka Kroef concentrated on the Hansa potato variety, a yellowish, firm cooking, and versatile potato with an outstanding taste. The selected potatoes are supplied by more than 200 arable farms, mainly from the Peel region of Brabant. After the harvest, the potatoes are processed into either chilled products with a short shelf life or chilled products for a long shelf life. The products, which are also adapted to the particular requirements of individual countries, are sold under the "Peka" brand name, as well as under the "own label" brands of various supermarkets. “We also supply other large customers in the food service sector, as well as smaller retail outlets under our own brand name,” adds Frans Habraken.
MULTIVAC packaging machines have been used at Peka Kroef for around 25 years. In order to be able to increase productivity, efficiency, and pack quality still further, as well as meeting the strong demand for the company's products, the decision was made to replace the previously used thermoform packaging machines with four new models of the R 535 type. “These machines offer a wide range of state-of-the-art features, which help us to achieve our ambitious objectives,” says Frans Habraken.
The integrated seal seam inspection system has proved to be particularly efficient. This makes a major contribution to guaranteeing that only perfect packs are delivered to customers, and therefore ensuring the optimum product shelf life can be achieved. The smallest product particles or air bubbles in the seal seam can cause leaks in the pack, and this means a reduced shelf life or premature spoilage of the product. “We do not want to leave anything to chance, when it comes to the quality of the product or pack. Since our company was founded, we have established an outstanding reputation with our customers in the catering and retail sectors, as well as with consumers. We therefore needed a system which could reliably detect faults in the seal seam and eject the reject packs,” explains Frans Habraken.
In conjunction with MULTIVAC, the decision was therefore made to equip the new high-performance packaging machines with the latest inspection systems, which would allow automated pack inspection even at very high output.
The catalogue of requirements for the overall investment was thoroughly ambitious. This meant the efficiency and flexibility of the packaging lines had to be increased, while at the same time maintaining the outstanding pack quality and long product shelf life. This was because the product range was no longer just restricted to different versions of pre-cooked and seasoned or unseasoned potatoes. The company was now also offering a wide range of speciality products, from potato gratin to roast potato dishes and rosti potatoes, which could be used as main meals, side dishes, or as the basis for consumers' own creations.
The requirements of maximum flexibility are met in full by the R 535 machines, since they are equipped with intelligent quick-change systems. The die change required for the three different pack formats, which are produced on the machines at Peka Kroef, can be performed extremely quickly, and machine downtime is therefore minimised as much as possible.
The wishes of Peka Kroef as regards the packaging concept have also been met in full - the company can pack the products in either MAP or under vacuum in all the different pack sizes. “And last but not least, we were able to further optimise the pack design so that we can now produce attractive and even more secure packs with less film - an important step in the direction of sustainability,” explains Frans Habraken.
A further benefit that is highly appreciated: An OPC interface is available via the MULTIVAC HMI 2.0 control terminal for comprehensive communication with other systems within the company. The linking of the production and packaging processes increases not only efficiency, but also ensures a more even product flow is achieved throughout the entire processing procedure.
A total of four new machines were installed. Two have been in use since 2017, and two more followed in 2019. They are equipped with visual inspection solutions from MULTIVAC Marking & Inspection. The labelling and marking specialist offers a comprehensive product range in this sector as well, which extends from simple inspection tasks right up to more complex or multi-functional tasks, and it therefore covers the entire spectrum of solutions for pack, label, and marking inspection.
The inspection systems were mounted directly on the outfeed of the thermoforming packaging machines. “Today at Peka Kroef any air bubbles or foreign particles, which have been trapped in the seal seam, can be detected automatically and with absolute reliability even at high output,” says Ton van den Bosch, Key Account Manager at MULTIVAC, explaining the benefits of the solution. Even at high speeds, the advanced image capturing technology enables razor sharp images to be transmitted and verified.
Other benefits also lie in the ease of operation via the central control terminal, since the settings or configurations can be called up directly when the particular recipe is loaded. The inspection results are transferred directly to the MULTIVAC Line Control, so that packs detected as reject can be tracked and then ejected reliably from the line.
At Peka Kroef there has been a very positive assessment of the investment decision: “Efficiency, productivity, sustainability, and the highest pack quality - the new thermoform packaging machines perfectly meet the requirements of our time,” says Frans Habraken in summary. He also praises the packaging specialist for its many years of cooperation: “MULTIVAC always thinks with solutions in mind. Together with MULTIVAC's comprehensive expertise in applications and automation, the well-established German thoroughness, which is used to meet every challenge, gives us the certainty that we have implemented the best solution with our investment.”
05.04.2020